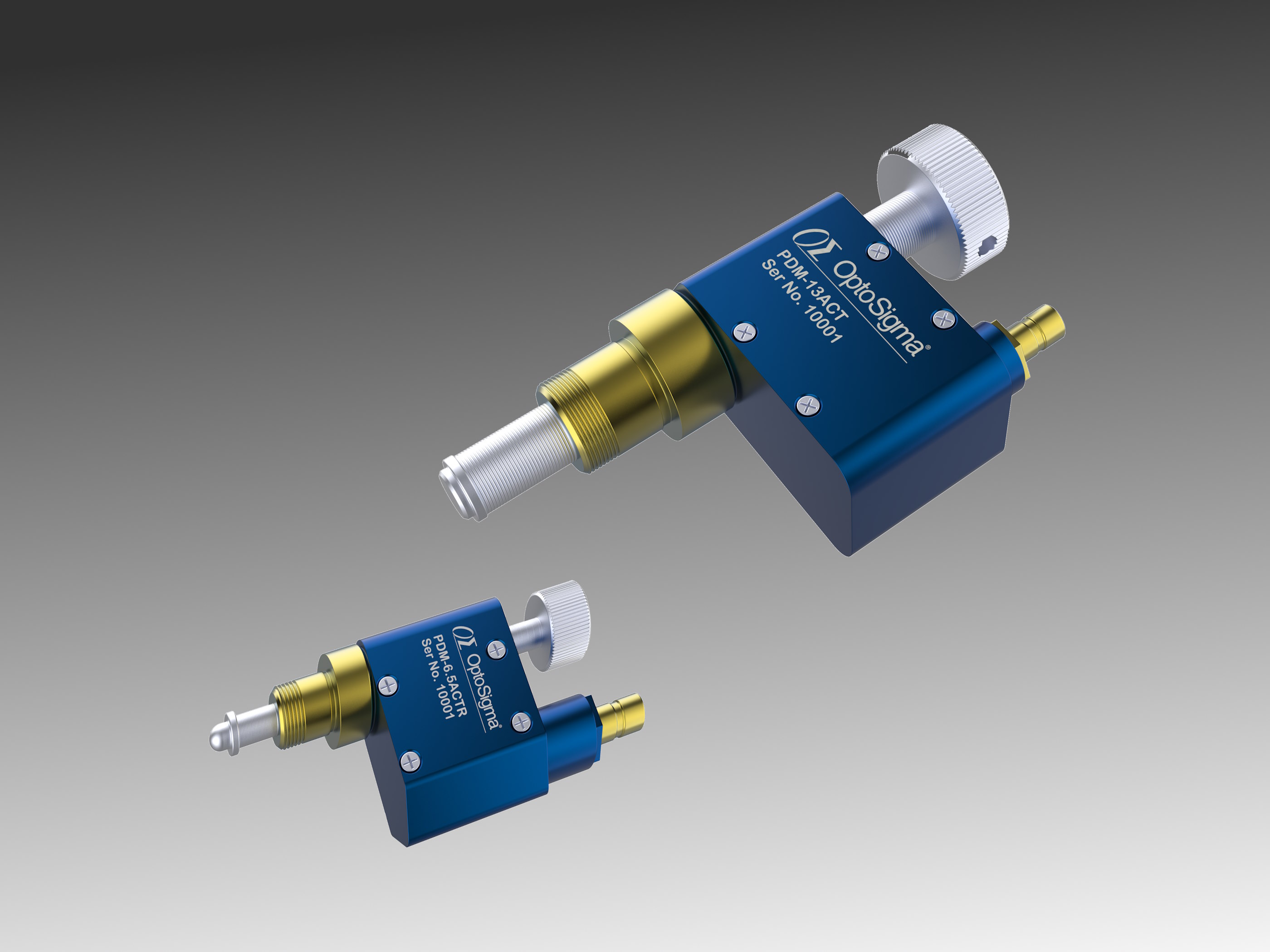
High-Resolution Piezomotor Actuators
Our piezomotor actuators are compact and provide extremely high-resolution incremental movement, as low as 20nm. The motion of these actuators relies on the structured, high-speed "vibration" of a piezo stack along with the force difference between the friction of a moving object (dynamic) vs. friction of a non-moving object (static). Recall that that friction on a non-moving object is higher than that of moving friction. In the motion process, the piezo is expanded slowly, enabling higher static friction, and this makes the screw rotate in a direction. Then, the piezo is retracted very quickly, for lower static friction such that the screw does not rotate. Applying this process repeatedly at a high rate causes the actuator screw to rotate continuously in a particular direction. Simply reversing the order of the fast and slow piezo expansion/retraction changes the direction of rotation, allowing the screw to move in the opposite direction. One of the key benefits of piezomotor actuation is that the static friction, which is in effect when the piezomotor is not operating, also acts like a locking mechanism which ensures excellent stability. Our PDM piezo actuators are available in two travel ranges, 13- and 6.5-mm and have industry-standard 9.5-mm and 6-mm diameter mounting interfaces allowing them to be drop-in replacements for standard micrometers. They also have ball-tip or flat-tip options. Another convenient feature of these actuators is that the electrical cable is conveniently removable. Please note that these actuators do not have internal feedback and therefore are open-loop. Vacuum compatible versions are also available. If your application needs different specifications we can customize our piezomotor actuators to your unique requirements.
Piezoelectric Actuator Guide
— Enabling Nanometer Positioning
1. What Is a Piezoelectric Actuator?
The Piezoelectric Actuator is a compact motion device designed to achieve ultra-high resolution positioning. The piezo replaces the micrometer head to convert a manual trenslation stage into a nanometer-level automated positioning system. It maintains stable positioning without the need for continuous power, making it suitable for applications that require high stability.
We offer fully assembled motion control solutions, including precision stages, mirror mounts, and integration services tailored to your needs.
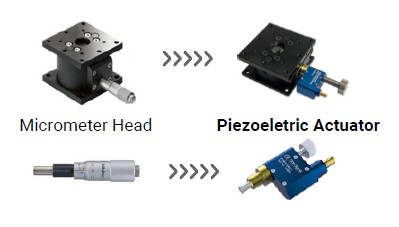
Key Features:
- Ensure Orthogonal Axis Movement
- Quick and Easy Upgrade
- Resolution of 30 Nanometers or Less
- No Continuous Power Needed
- Virtually No Backlash
- Seamless Integration
Specifications | ![]() |
![]() |
---|---|---|
Standard Travel | 0 - 6.5mm (Max. 9mm) | 0 - 13mm (Max. 18mm) |
Minimum Movement | <30nm | <25nm |
Maximum Speed | 1.5mm/min | 1.5mm/min |
Maximum Load Capacity | 15N | 30N |
Weight | 0.02kg | 0.05kg |
Mounting Shank Diameter | 6mm | 9.5mm |
Dimensions (mm) | 41 x 21.6 x 8.2 | 61 x 31 x 15.1 |
Tip | Flat/Ball | Flat/Ball |
2. How It Works?
The Piezoelectric Actuator operates through a piezoelectric inertia rotation mechanism inside the housing, which rotates the screw shaft to generate precise thrust and displacement.
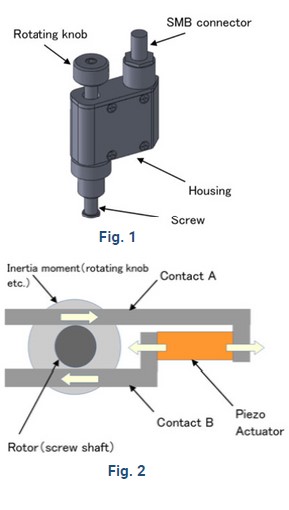
Figure 1: External Structure
- The motor consists of a rotating knob, housing, screw shaft, and an SMB connector, converting rotational motion into precise linear displacement.
Figure 2: Working Principle
- The Piezoelectric Actuator rapidly expands and contracts under high-voltage signals, generating force.
- The rotor attached to the screw shaft is pressed against Contacts A and B to create static friction.
- If the force from the actuator is less than the static friction, the rotor moves smoothly; if greater, controlled slippage occurs.
- The moment of inertia stabilizes the motion for precise control.
- Once positioned, the motor holds its place without requiring continuous power.
Controller and Connection Example with Piezoelectric Actuator
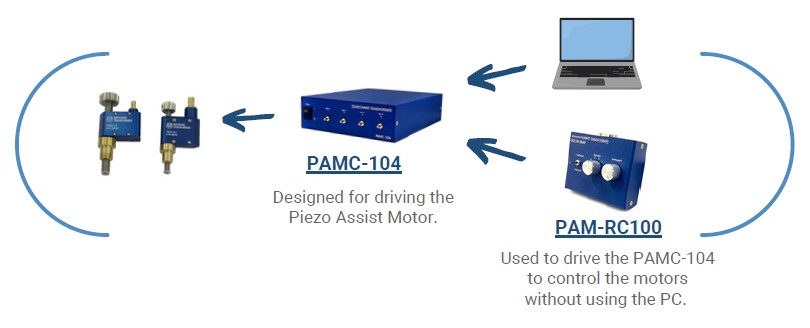
3. Application Cases
- Precision Stage
3-axis (X-axis, Y-axis, Z-axis) precision stage equipped with a Piezoelectric Actuator.
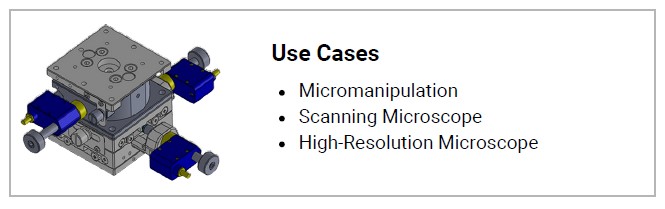
- Mirror mount
2-axis (X-axis, θ-axis) mirror mount equipped with a Piezoelectric Actuator.
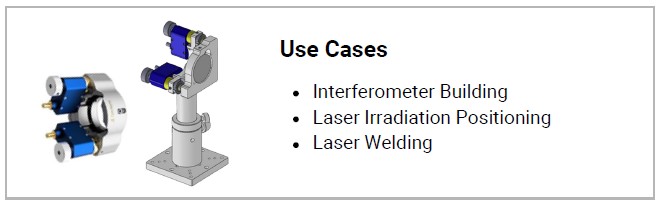
Closed-Loop Feedback
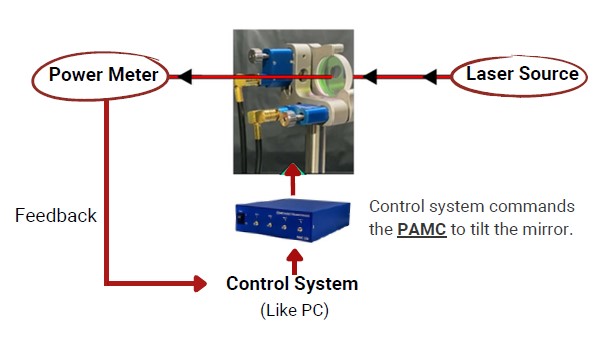
Conceptual Scheme of the Mach-Zehnder Interferometer
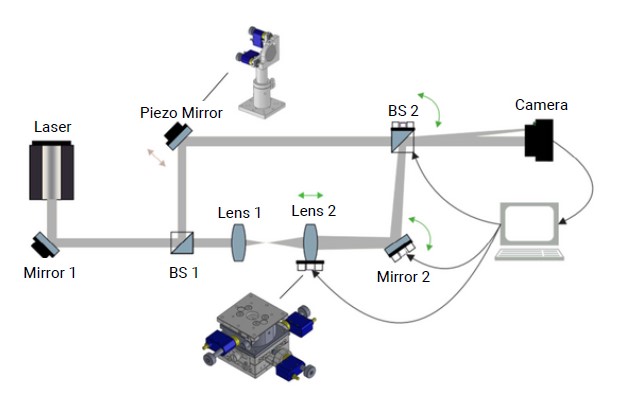
GET STARTED WITH PRECISION MOTION
- Upgrade to high-precision automated control with our Piezoelectric Actuator solutions.
- Whether you need a standalone actuator or a fully integrated motion system, we provide customized solutions for your application.
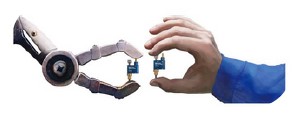
Speak with our experts for technical support or integration guidance.
Get a customized solution tailored to your needs.